The Business
Attwood, a Navico Group Brand, is the world’s largest producer of marine accessories. For more than 100 years, Attwood has been the unquestioned award-winning leader in design, development, testing, and manufacturing of the highest quality boat parts and accessories for the marine industry.
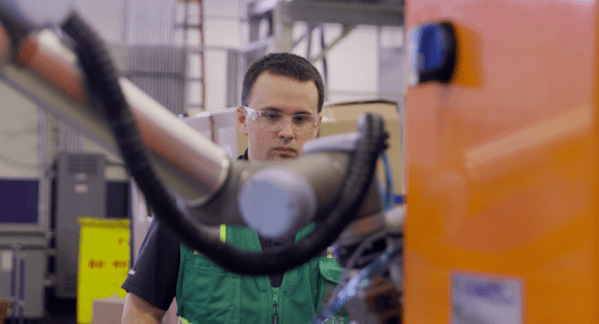
The Challenge
As competitors moved manufacturing overseas, Atwood was struggling to stay cost competitive. They were determined to keep production and jobs in the US, but their high-mix low-volume manufacturing made robotic automation expensive and difficult to justify – especially since they had no automation experience. They sought a future-proof solution that would allow them to reduce manufacturing costs and keep manufacturing in the US.
The Solution
Attwood chose to build their automation around Forge OS – as this programming platform could support the cobots they’d deploy out of the gate, as well as the industrial arms they might need in the future. Forge OS presented a user-friendly programming environment that would allow them to program their own automation and robotics tasks – despite their lack of automation experience. The user-friendly programming interface (Task Canvas) would provide their machine operators with a tool they could comfortably learn to operate.
Attwood began automating production with a mobile robotic solution powered by Forge OS. It featured a cobot from Universal Robots fitted with a 2-finger Schunk gripper mounted to a mobile base. It enabled them to implement collaborative automation in their domestic manufacturing facilities – bringing down costs, increasing competitiveness, and keeping their manufacturing in the US.
Two years after automating various production tasks with their Forge OS-powered mobile cobot system, Attwood was ready to automate product testing. The new application would require more payload than their UR cobot could offer. They also wanted to test at speeds that exceeded the capabilities of their cobot. They needed an industrial arm. The brand agnostic nature of Forge OS enabled them to choose the right robot for this new task – without brand constraints. Attwood chose a FANUC R-2000iB powered by Forge OS. Adding a new robot brand to their production floor was seamless due to Forge OS’s brand-agnostic operating system and programming platform. And, for about the same cost as a small collaborative robot, Attwood was able to add an industrial arm with significantly more payload, reach, and speed.
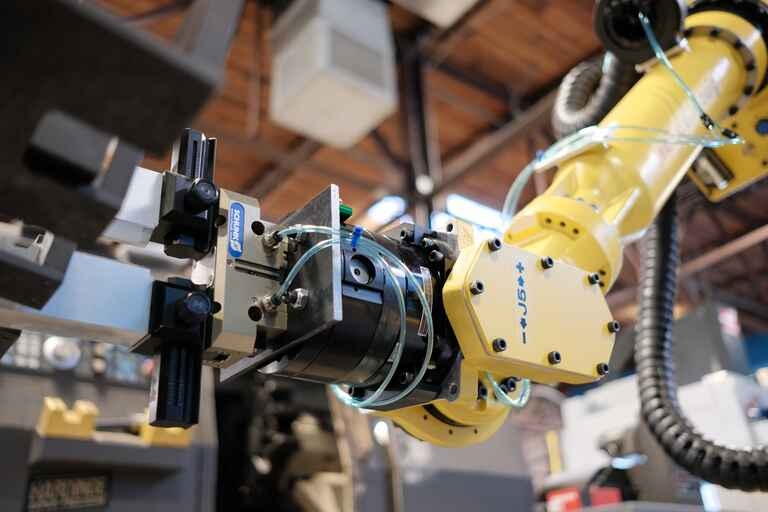
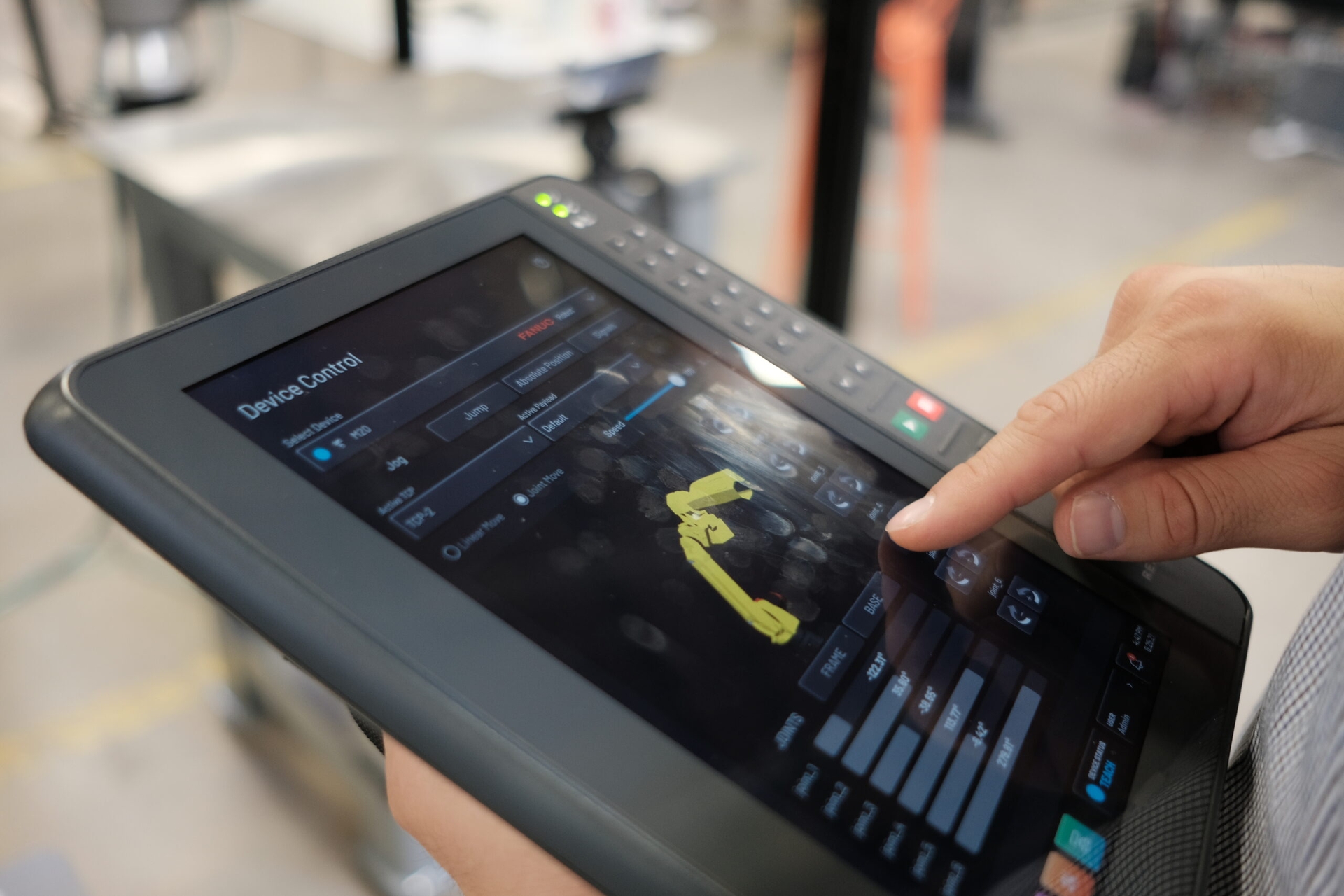
The Results
Short Term: Forge OS-Powered Mobile Robotic Solution
The flexibility of their Forge OS-powered mobile robotic system (like those offered by READY partners Futura Automation, FINCH Automation, and Accufacture) enabled Attwood to quickly deploy automation, improving production efficiency across multiple workstations, and across a wide range of parts. The form factor enabled the mobile robotic solution to be easily moved between workcells as projects demanded, but the programming environment of Forge OS was the real game changer. Forge OS’s No Code programming environment allowed Attwood to quickly program for new parts and manage change over – both of which are critical in their high-mix low-volume environment. Programming was not a barrier, nor was it a timesink.
Forge OS also enabled machine operators and other members of their production team with zero automation experience to operate robots and automation equipment. They were not dependent on a single “expert” to unlock productivity gains with their Forge OS-powered robotic solution. Attwood Marine was able to spread ROI across many different product lines, and more rapidly achieve ROI. Equally important, the intuitive programming environment of Forge OS enabled Attwood’s team to program for new tasks, update for new parts, start and stop cycles, and recover the system. With Forge OS they owned their automation journey.
Long-Term: Forge OS-Powered FANUC Industrial Arms
Although the No Code programming environment of their Forge/Station unlocked automation for Attwood – the true power of Forge OS became apparent when they were ready to add an industrial arm to their production floor. New product testing required payload and speed that exceeded the capabilities of their collaborative system. Having standardized on Forge OS, stepping up from a UR cobot to a FANUC industrial arm was a seamless transition.
Forge OS enabled Attwood to choose the right arm for their new application with no limitations to brand. Attwood chose a FANUC R-2000iB, an industrial arm with a 100kg payload. Tasks programmed on their cobot were ported over to their new industrial arm and touched up – reducing programming time significantly. Once a few waypoints were updated, they were off and running. Programming new tasks was painless for their team, as the Task Canvas programming interface didn’t change at all from collaborative UR to industrial FANUC.
Attwood has since added another FANUC R-2000iB powered by Forge OS.